11.07.2018 Stipo Nad
ShareQuelle: ve_ro_sa / shutterstock.com
In meinen Blogbeiträgen berichte ich häufig über die Schwierigkeiten, die Maschinen- und Anlagenbauer mit einer termintreuen Produktion haben. Verspätete Lieferungen sind in dieser Branche keine Seltenheit, stoßen aber zunehmend auf weniger Akzeptanz beim Kunden. Damit gehört der herumeilende Terminjäger in der Einzel- und Kleinserienfertigung quasi mit zum Inventar. Wie die Verantwortlichen mit der Priorisierung verschiedener Arbeitsgänge genau umgehen, kann je nach Firma variieren. Von auffälligen Stempeln bis hin zu roten Karten gibt es eine weite Palette an Kennzeichnungen für unterschiedlich priorisierte Aufträge, darunter die gefürchteten Chefaufträge. Hauptsache, “Prio A++“ wird als erstes erledigt.
Doch obwohl viele Maschinenbauer solche Kennzeichnungen der Prioritäten für die gängige und damit auch bewährte Methode halten, heißt das nicht, dass es auch eine effiziente Vorgehensweise ist. Denn durch diese Art der Priorisierung wird lediglich die Termintreue eines Auftrags verbessert, eine Verbesserung der gesamten Produktion bleibt jedoch aus.
Nicht manuell planbar
Ein Umdenken weg von der täglichen Routine in der Fertigungs- und Montageplanung zu einer übergreifenden, dynamischen Priorisierung müssen viele Unternehmen häufig erst lernen, und vor allem umsetzen. Das ist kein Vorwurf. Denn die Komplexität, die tausende Aufträge mit wieder tausenden Arbeitsgängen mit sich bringen, ist einfach nicht manuell zu planen und steuern. Die Unterstützung durch ein ERP-System reicht hier nicht mehr aus. In der täglichen Arbeit führt dies häufig dazu, dass Termine letztendlich kurzfristig umgeschmissen und nach Erfahrungswerten des jeweiligen Mitarbeiters priorisiert werden.
Eine zentrale Steuerung fehlt
Ein weiteres Problem bei Umplanungen aufgrund von beispielsweise verzögerten Lieferungen oder Maschinenausfällen: Jeder Bereich wie Montage oder Fertigung plant lokal für sich neu. Eine übergreifende Übersicht über die Aufträge fehlt. In der Regel bestimmt der Kunde oder das Bauchgefühl des Fertigungsmitarbeiters, welcher Auftrag wichtig ist und welche Priorität dieser erhält.
Die Folgen sind, dass sich jeder Bereich aus eigener Sicht gesondert optimiert und dabei nicht die bereichsübergreifenden Zusammenhänge der Aufträge berücksichtigt. Das Ergebnis sind Unmengen an angearbeitetem Material in der Montage trotz wachsender Fehlteillisten. Denn auch wenn der Terminjäger dafür gesorgt hat, dass „sein“ Bauteil pünktlich in der Montage ankommt, kommt es häufig vor, dass die restlichen Bauteile letztendlich fehlen. Erst mit Hilfe von Auftragsnetzen können alle Aufträge abgebildet und so ein Blick auf die Relationen zwischen verschiedenen Aufträgen ermöglicht werden.
APS-Systeme steuern zentral und intelligent
Intelligente Produktionsplanungssysteme helfen, einen übergreifenden Blick nicht nur auf die Produktion, sondern auch auf die ebenfalls am Prozess beteiligten Bereiche wie Einkauf und Montage zu werfen. Nur so ist es möglich, die Prozesse ganzheitlich über die gesamte Wertschöpfungskette zu optimieren. Steigende Kundenanforderungen, wachsende Variantenvielfalt und der zunehmende Druck einer termintreuen Lieferung erschweren eine reibungslose Planung der Produktionsprozesse im Maschinen- und Anlagenbau. Hinzukommen Zukaufteile, die fremdproduziert werden.
Da der Produktionsprozess bereichsübergreifend ist, sollte es dementsprechend auch der Planungsprozess sein. Dafür müssen zentral alle Prozesse aufeinander abgestimmt koordiniert und gesteuert werden.
Aufgrund mangelnder Informationen aus den anderen Abteilungen liegt der Produktionsmitarbeiter mit seinem Bauchgefühl nicht immer richtig. Intelligente APS-Systeme berücksichtigen bei der Auftragspriorisierung alle Gegebenheiten in der Produktion und können so abteilungsübergreifend die Prozesse optimieren. Diese ganzheitliche Optimierung führt zu:
- einer vorausschauenden, auslastungsorientierten Produktion, bei der das richtige Material zur richtigen Zeit am richtigen Ort zur Verfügung steht,
- Reduktion von Work in Progress und Rückständen,
- Verringerung von Durchlaufzeiten und Planungsaufwand durch eine automatische, optimierte Reihenfolgeplanung,
- frühzeitige Vermeidung von Engpass-Situationen durch transparente Prozesse,
- höhere Produktivität durch weniger Stillstandzeiten und eine optimale Maschinen-Auslastung.
Fazit
Viele Maschinen- und Anlagenbauer kennen die vielfältigen Herausforderungen von Losgröße 1 und deren komplexe Fertigung. Dennoch verlassen sie sich häufig noch auf ihr Bauchgefühl und jahrelange Routine in der Planung der Aufträge. Doch nur im Zusammenspiel mit einer zentralen Steuerung und Planung ist es möglich, diesen Herausforderungen wirklich gerecht zu werden und schnell auf geänderte Kunden- und Marktanforderungen zu reagieren. Eine marktsynchrone Produktion entsteht nicht aus dem Bauch heraus oder durch einen besonders schnellen Terminjäger, sondern durch eine übergreifende Planung vom Einkauf über die Produktion bis hin zur Montage. Intelligente Planungssysteme behalten hier den Überblick über tausende Aufträge – und sorgen für eine übergreifende Optimierung ohne Verspätungen.
Wie priorisieren Sie Aufträge in der Fertigung? Kennen Sie die genannten Schwierigkeiten?
ÜBER UNSERE EXPERT:INNEN
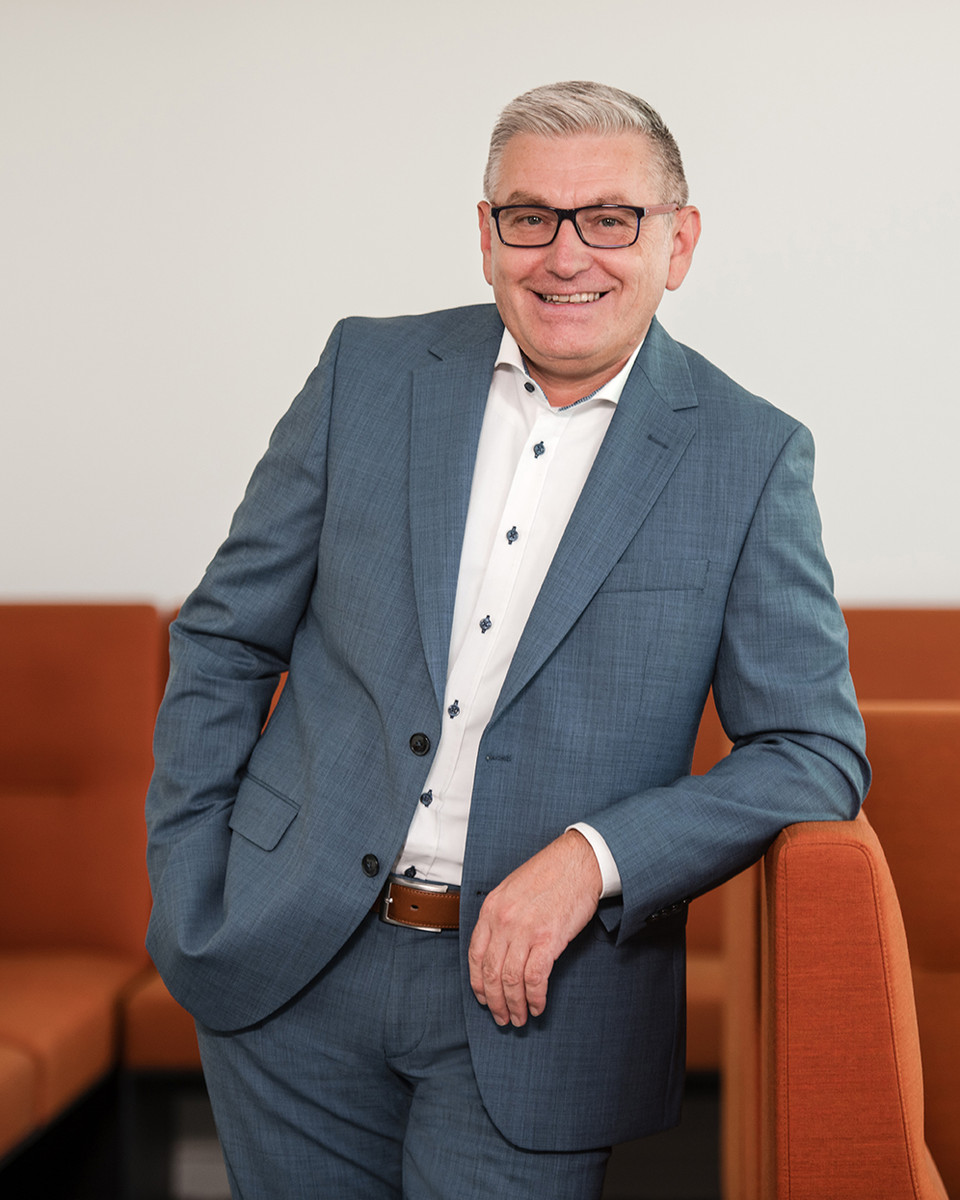
Stipo Nad
Head of Business Development Produktion
Stipo Nad ist seit 2001 bei INFORM tätig und beschäftigt sich hauptsächlich mit den Themenschwerpunkten Advanced Planning & Scheduling sowie Produktionsplanung im Maschinen- und Anlagenbau und anderen Einzel- und Kleinserienfertigern.