Apr 14, 2025 Zdravka Ley
ShareImagine the internal flow of materials like the flow of road traffic: While the forklift acts flexibly, like a car, and transports material on demand, the tugger train takes on the role of a scheduled bus - reliable, planned and with significantly more capacity per journey.
Tugger trains bundle several transport orders into one journey and thus not only reduce internal traffic, but also CO₂ emissions and energy consumption. In times when sustainability and resource protection are becoming increasingly important, the use of tugger trains is becoming a strategic decision for sustainable logistics.
What is a tugger train?
A tugger train is a means of transport for internal material flow. It consists of a towing vehicle with one or more trailers and transports several load containers simultaneously on a fixed route through the plant - in contrast to a forklift truck, which usually handles individual transport orders flexibly.
Tugger trains are particularly suitable for horizontal material transport between the warehouse, incoming goods and production. Their strength lies in the regular, plannable supply of production lines or assembly stations - in line with the milk run principle: one loading point, several unloading points, but only a single, efficient journey.
Tugger trains on the rise: advantages for logistics, production and the environment
The use of tugger trains is steadily increasing - and for good reason. More and more companies are relying on these plannable transport units to make their intralogistics more efficient, transparent and sustainable. In many cases, the tugger train is already the backbone of a standardized line supply - and an important step on the way to a forklift-poor or even forklift-free factory. But what are the specific advantages?
Here are the most important advantages at a glance:
- Efficiency up, costs down
By bundling several transport orders into one journey, capacities can be better utilized and empty runs can be reduced or avoided. Coordination and driver costs are also significantly reduced. - Less traffic, more safety
Fewer vehicles on the factory premises means fewer disruptions, a lower risk of accidents and smoother processes - a real benefit for production and work safety. - Fewer emissions, more responsibility
Fewer journeys, less energy consumption, fewer emissions: Tugger trains actively contribute to improving the environmental balance - especially in combination with electric tractors. - Smooth supply instead of bottleneck alarms
Fixed cycles, defined routes and standardized processes ensure predictable deliveries and stable processes. Bottlenecks and supply interruptions can be systematically avoided. - Easy scalability
Tugger trains can be flexibly adapted - whether simple line supply or complex milk run concepts. Cycle frequency, routes and resources can be configured as required. - Faster material availability
Optimized routes and targeted timing shorten transport times - materials arrive faster where they are needed.
Tugger trains with brainpower: Why optimization is crucial
As convincing as tugger trains are - in practice, there are various challenges that can quickly become an efficiency inhibitor without targeted control. Firstly, tugger trains are usually dependent on fixed routes. Spontaneous changes to the sequence are difficult to integrate, especially if several stations are linked together per journey and delays at one point throw the entire cycle out of sync. There are also system-related restrictions: Conventional tugger trains are only designed for horizontal movements; reversing or travelling uphill is only possible to a limited extent.
It also quickly becomes complex in organising: Which orders can be sensibly combined? How can the loading and unloading sequence be optimized - especially for tugger trains that can only be loaded and unloaded on one side? In many companies, route planning is still done manually or with the help of Excel - a time-consuming and error-rich process that hardly scales. If unplanned changes, urgent individual orders or late deliveries are added to the mix, fixed driving cycles quickly become unbalanced. As a result, capacities remain unutilized, routes are unnecessarily extended and there are frequent aisle changes in the warehouse or production.
Without intelligent management, the full potential of tugger trains can hardly be utilized. This is precisely where the SYNCROTESS intralogistics management system comes in.
Intelligent tugger train optimization with SYNCROTESS
Modern intralogistics requires more than just fixed schedules. Particularly in dynamic production environments, intelligent, software-supported tugger train planning is the key to efficiency. The SYNCROTESS intralogistics management system plans and controls tugger trains dynamically, demand-oriented and route-optimized - instead of rigid timetables, intelligent decisions are made in real time.
In route train operations, it becomes particularly clear how SYNCROTESS seamlessly combines planning, control and efficiency:
- Route bundling & aisle optimization
Transport orders are automatically combined into sensible routes - taking into account loading and unloading sides, lane sequences, positions and priorities. The aim is to drive through as few aisles as possible, use the shortest routes and optimize resource utilization. - Automatic slot and route allocation
The software not only calculates the optimum sequence of unloading points, but also which order belongs in which slot of the tugger train - in line with the route and the loading/unloading logic. - Flexible for every use case
Whether loading by forklift or self-loading by driver - SYNCROTESS adapts to real processes and also maps individual tugger train concepts. - More transparency, less effort
Manual planning, Excel lists and gut instinct are a thing of the past. Operational control is transparent, scalable and efficient - integrated into the overall plant logistics process.
What's more, SYNCROTESS is as flexible as logistics itself. The software can be used exclusively for tugger trains or as part of a comprehensive system that also intelligently coordinates forklifts, AGVs and other resources. As a specialist for hybrid fleets, SYNCROTESS ensures perfect interaction between manned vehicles and automated systems.
Conclusion: Rethinking tugger trains
Today, tugger trains are far more than just an alternative means of transport to forklift trucks. They are a central element of modern plant logistics - wherever efficiency, predictability and sustainability are required.
For tugger trains to realize their full potential, they need more than just good hardware: they need an intelligent interplay of planning, control and transparency. This is precisely where SYNCROTESS comes in - with a solution that not only controls tugger trains, but also integrates them into existing processes in a targeted manner and continuously optimizes them.
If you want to make your material flow fit for the future, you no longer need to think about tugger trains in circles - but as the strategic axis of smart, digital intralogistics.
About our Expert
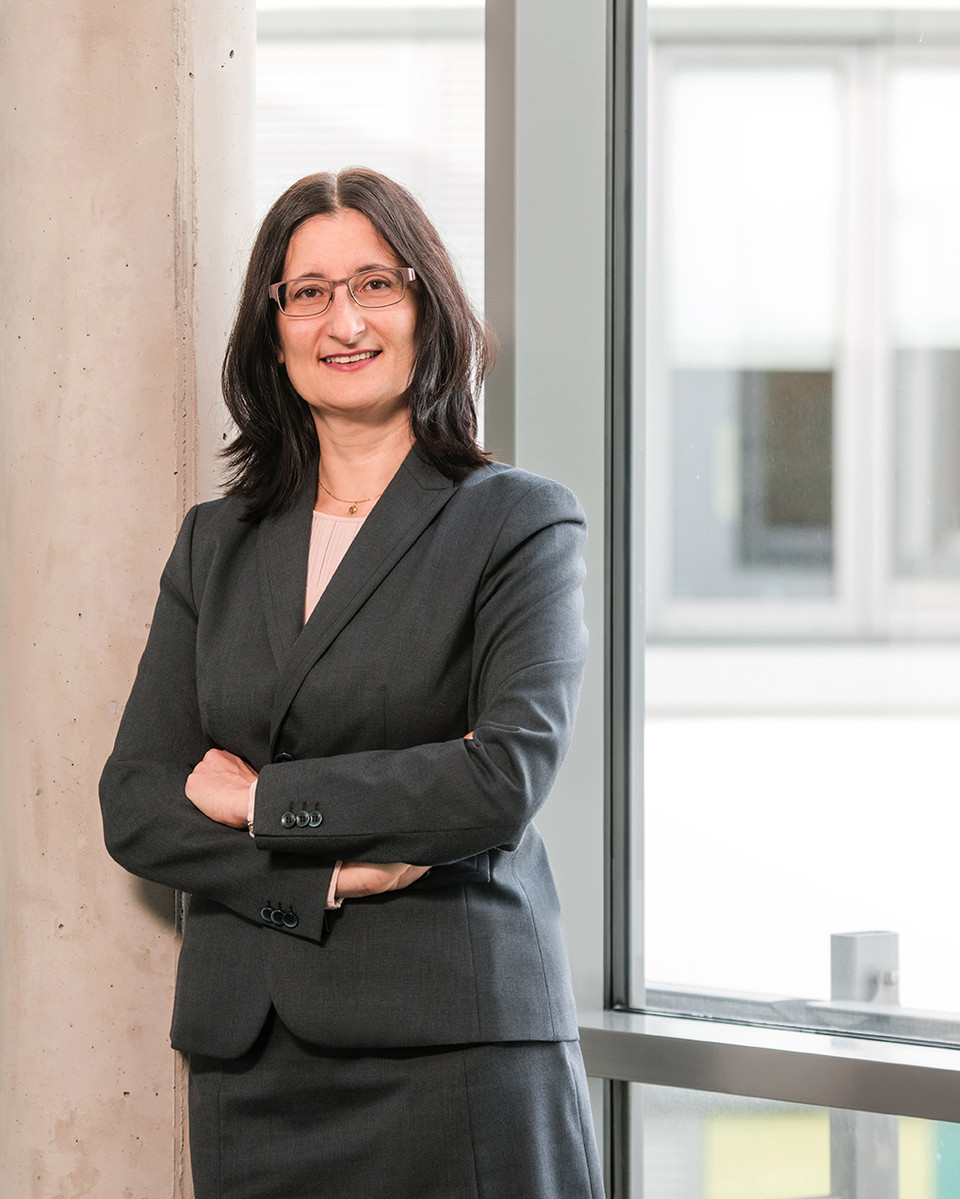
Zdravka Ley
Marketing Manager
Zdravka Ley started working for INFORM in 2002 and is focused in topics around the optimization and sustainability of delivery and internal transport logistics.