MTU Aero Engines AG centralizes in-plant logistics with INFORM software
MTU Aero Engines AG is Germany's leading engine manufacturer. Its core competencies lie in low-pressure turbines, high-pressure compressors, turbine center frames, and manufacturing and repair techniques.
MTU has been using the Intralogistics Management System SYNCROTESS to optimize its multi-stage transport chains in in-plant logistics since 1993. Many years of working with INFORM's AI-based system helps the company to respond to the increasing complexity of logistics. In addition, SYNCROSUPPLY, a cloud-based solution time slot and yard management, has been in operation since 2021 to reduce throughput times of trucks and increase transparency of inbound traffic.
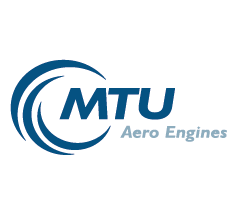
High delivery reliability
"With the innovations, internal delivery reliability was increased from 89% in 2020 to 93% in 2022, despite greater complexity and increased volumes."
Florian Wohlgemuth, Project Manager Logistics Planning, MTU Aero Engines AG
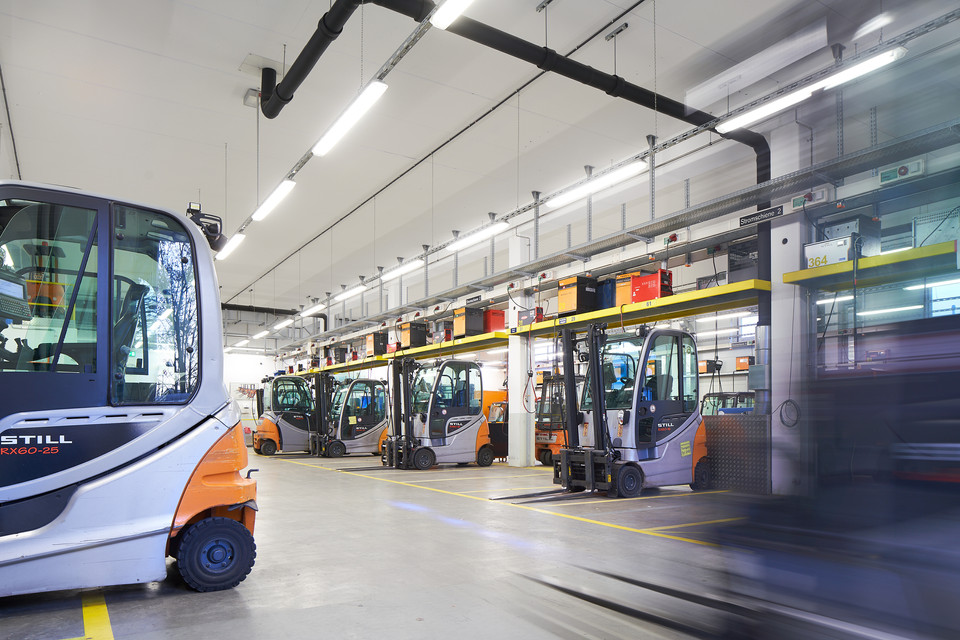
The Intralogistics Management System handles no fewer than 560,000 transport orders a year for the engine manufacturer. Between 2020 and 2022, the number of orders increased by more than a quarter, partly due to rising production volumes. For decades, SYNCROTESS has served as the single source of truth for in-house transportation at MTU Aero Engines AG (MTU) in Munich. In order to meet changing logistics requirements and introduce new functionalities, in 2019, MTU decided to upgrade the system to the latest product version 10, and reintroduce SYNCROSUPPLY as part of an internal modernization project.
The software company and MTU, which develops, manufactures, and maintains engines consisting of 1,200 or more individual parts for commercial and military aviation, have been working together since 1993.
Real-time planning
As a central logistics system, SYNCROTESS dynamically calculates optimized handling sequences for forklifts, electric trolleys, trailer transports, and other means of transport in real time. As soon as the system registers an order - 99 percent are generated in the ERP system - and there is a change or disruption, the system reschedules within seconds. The algorithms schedule on the basis of all recorded orders and actually available resources; at MTU, around 30 vehicles simultaneously. Their optimization assigns the orders to vehicles in such a way that their processing is optimally synchronized with reported order priorities, deadlines, loading capacities, and short distances, as well as achieving a good and evenly distributed workload throughout the day.
One of the most important selection criteria for the INFORM Intralogistics Management System was its ability to map multi-stage transport chains, such as cross-hall warehouse and yard transports or site-to-site transports within the internal supply chain. MTU realized cost savings of around 30 percent in the transport area and an ROI of less than one year in the first few years after the initial introduction. However, the scope and complexity of the planning have increased enormously since then: instead of the 60 items previously included in the planning, over 400 items are now taken into account. Since then, the production logistics have been expanded to include, for example, transportation across different production stages or the integration of a fully automated high-bay warehouse. In recent years, several small-scale processes have been added.
Intralogistics set up for the future
Transport volume has increased significantly in recent years, says Florian Wohlgemuth, Project Manager Logistics Planning (TLLP) at MTU in Munich. Various drivers have led to an increased production volume, but also the expansion of algorithmic planning with the INFORM systems. For example, various external locations were gradually connected and new transport processes were mapped. These include, for example, the transportation of small parts, transportation from the tool dispenser, the filling of gas cylinders, archive trips, and the internal goods delivery service.
"We aimed to achieve the same level of transparency in these newly integrated processes that we have established in production supply with SYNCROTESS," says Wohlgemuth. MTU's modernization project also included the expansion of WIFI availability throughout the plant. Instead of using the old narrowband radio network and black-and-white monitors, forklift drivers now receive transport orders from SYNCROTESS via WIFI on more modern, mobile end devices with increased usability. The "Site-Logistics" app developed by INFORM shows drivers which order they should drive next. According to Wohlgemuth, the app is particularly helpful for new employees, as they can use a map created with Open Street Map to view start and destination positions, the transport network, and sensible, feasible routes. The scanning processes have also been simplified by the app, which is important for continuous goods traceability. They now take place via the same mobile devices. And if a job cannot be completed, the company saves unnecessary additional trips thanks to the app, as the manual deletion of an order is immediately taken over and included.
"With our modernization measures, we are enabling mobile scanning processes for the small parts processes and better traceability across all process steps," he adds. "Enquiries about where a particular transport is, or where material is currently located, are now close to zero. To achieve this, we combined a digital track & trace system at store floor level with the Intralogistics Management System." The latest version of SYNCROTESS also makes it much easier to adjust master data and optimization parameters. Planning has become more precise, for example, by allowing certain resources to be limited to specific areas. Whereas in the past the focus was more on reducing distances, nowadays adherence to delivery reliability, especially in the direction of dispatch, is the top priority. With the innovations, internal delivery reliability was increased from 89% in 2020 to 93% in 2022, despite greater complexity and increased volumes.
Next, MTU tested the control of driverless transport systems (AGVs) from various manufacturers in the indoor and outdoor areas of the Munich plant using the INFORM system. The vision is an optimized mixed operation of human-controlled forklifts and AGVs, whose transport sequences are planned in an integrated system.
The quality of the master data should also be improved further. The latest version of SYNCROTESS provided MTU with a new simulation module in which master data changes can be simulated, taking into account the consequences for various key figures, such as throughput times. The impact of such changes in the ever-growing transport network is difficult to monitor manually. In the course of 2023, Wohlgemuth would like to continue working on reducing empty runs and also focus on sustainability in logistics through the careful use of resources.
Ramp optimization
In the past, incoming truck traffic from around 500 service providers mainly reached MTU in the mornings, with a total of around 60 deliveries per day at four ramps. Delivery peaks presented the company with logistical challenges, which led to waiting times for the truck drivers during employee breaks. As there are also construction sites on the factory premises, the volume of traffic in the factory should be reduced and incoming forwarders have to go through certain registration and security processes, the waiting area for trucks had to be moved to the road outside the factory premises. MTU opted for SYNCROSUPPLY from INFORM in order to distribute the workload at incoming goods more evenly throughout the day, to reduce waiting and throughput times, and to create end-to-end transparency.
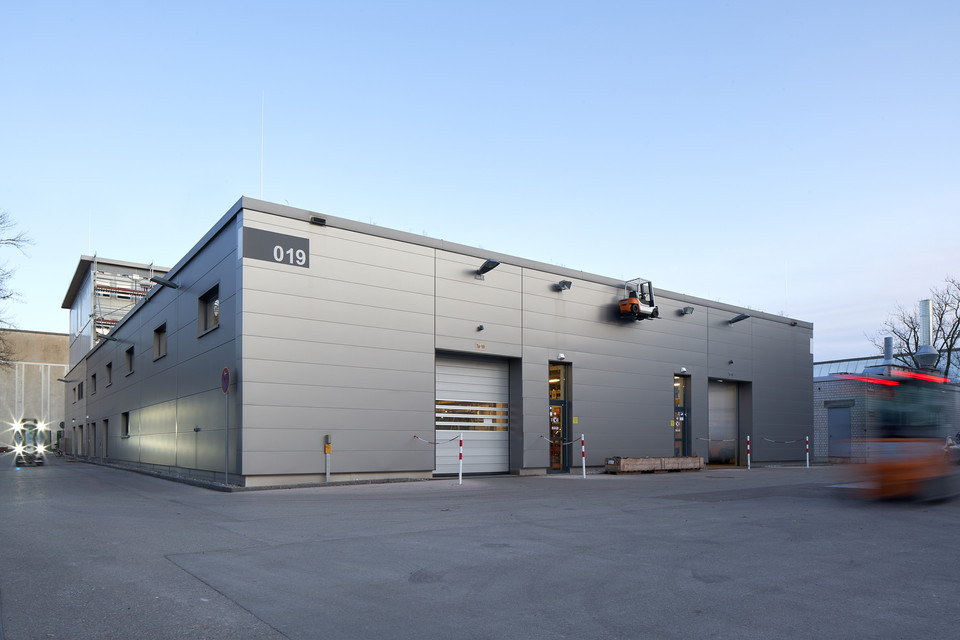
The system is used to book and plan time slots for incoming trucks as well as to optimize the allocation of these to the correct ramp. From now on, every incoming goods shipment is stored in the system with a journey. Forwarders and their subcontractors who regularly call at MTU log in via a web-based portal to announce their journey, transmit data about the freight, and book a suitable time slot. This is particularly attractive for contracted suppliers who deliver general cargo and want to avoid waiting times as they have other customers to visit on the same day. Anyone who arrives spontaneously at the gate is allocated a time slot on site. This cannot be avoided in all cases, as many freight forwarders only visit MTU once or very rarely. Overall, however, Wohlgemuth plans to increase the proportion of pre-booked time slots to between 50 and 60 percent. Automated time slot allocation is also planned.
In addition to the planned equalization, which was already clearly noticeable shortly after the system was introduced in 2021, the company is also generating more and more data on inbound traffic, which can be used in the future for information to authorities, capacity utilization forecasts, or the needs-based provision of forklifts and drivers, for example. Once you have received your time slot, you can register at a self-check-in terminal that is connected to the INFORM system. This is followed by identity and sanction list checks before the driver is allowed to return to the truck with a pager. If the correct ramp is available for the relevant time slot, the truck is called up and guided through further processing on site.
"The volume will increase in the future and waiting times will become longer," predicts Wohlgemuth. "We are already preventing this now. We have transparency about who is in the plant, when and for how long, handle transports more efficiently, and have been able to significantly improve our throughput times: from an average of 56 to 46 minutes." The logistics manager says that, despite growth, the aim is to maintain and further improve these processing times.
GOALS ACHIEVED
- Continuous traceability of the material
- Increase in internal delivery reliability from 89% to 93%
- Further reduction of empty runs
- Visualization of all transport processes including the internal goods delivery service
- Significant shortening of throughput times from 56 to 46 minutes
- Reduction in the volume of traffic on the factory site
- Levelling of delivery peaks
- Homogenous utilization of incoming goods
- Concictent transparency in the yard