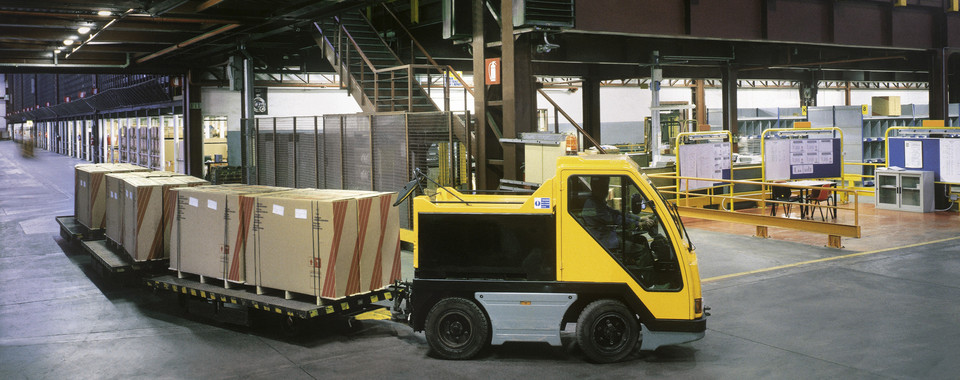
Apr 14, 2025 // Zdravka Ley
More than just in a circle: How tugger trains are changing internal logistics thanks to intelligent management
Why intelligent tugger train optimization is crucial.
Jan 19, 2017 Luisa Walendy
ShareSmart glasses, autonomous robotics and other digital technologies are increasingly gaining a foothold in production and logistics. In particular, the automotive industry is speeding toward Logistics 4.0. With millions of parts making their way to the production line, it is imperative that they show up at just the right moment in order to keep the line flowing smoothly.
For this reason, the automotive group Audi would like to bid farewell to the assembly line production. In the future, car bodies will be digitally interlinked and moved autonomously within the factory. These autonomous transports will make their way through individual fitting stations within the factory where components will be installed. This way, time and money will be saved.
When such futuristic technologies are introduced, most processes in production and logistics will be widely digitalized; these processes will be more visible and traceable than they already are. A good example, where transparency is still failing in logistics, is in internal logistics. Only a select few of those responsible in this area know exactly where the material needed for production is currently located. For this reason, digitalization is needed to increase transparency. A survey conducted by the logistic supplier Hermes proves that 46% of respondents with more than 250 employees already experience effects of digital networking and automation within their supply chains. However, 42% of large companies say their supply chains continue to be non-transparent in many areas. 76% of those businesses see the best opportunity for Logistics 4.0 through increasing transparency.
Why is the lack of transparency so high in internal logistics?
Transport within the factory often takes place without central control or pre-determined plans. In this case, transparency and an overview of the material movements within the factory are obviously falling by the wayside. Through the lack of transparency, quick and appropriate reactions for unplanned transportation requirements are impossible to achieve. Because plans cannot react accordingly, materials for production will be delivered too late. Additionally, it will result in many unnecessary trips and create inefficiency.
Therefore, modern transport management systems should ensure that all transports are planned in real time and that it is evident where transport orders should be situated at all times. This will result in shortened lead times, an optimized utilization of resources and a reduction in driving distance, which in turn will considerably improve timeliness. Furthermore, there will be no complaints throughout production, and customer orders will no longer be affected by a lack of transparency.
A transport management system is worthwhile - even for few forklift trucks
At first, this sounds good to a logistics specialist. However, investing in a transport management system and the cost of implementing it is not always worthwhile, especially for companies with few forklifts. Even with an increase in transport orders, the expense and cost of such an IT project is critically perceived. This is usually the first thought of many companies. However, you do not have to be an automobile manufacturer for a long period to digitalize your production and logistics, and thereby create transparency. Companies with few transport orders can, for example, use cloud solutions in order to avoid high investment costs and long projects. This is because these applications do not require the installation of servers. Cloud solutions can also be flexibly scaled in interim peak times.
Conclusion
The lack of transparency in supply chains is a problem. In logistical processes like internal logistics, the status of current orders are frequently missing. Transport management systems can help create a detailed overview of these transport situations. Information on transport orders, appointments, status and capacity is stored centrally and is available to be accessed anywhere, at all times. As a result, reactions to unexpected incidents in production and logistics will be enhanced in internal logistics. Empty trips and lead times can be minimized while resource capacity will be maximized. In particular, smaller businesses with fewer transport means can find a reasonable method to improve their internal logistics and production. Logistic 4.0 does not consist of only autonomous robotics, vehicles or virtual reality.
How do you optimize your internal transport and material flow? Do you work spontaneously or with planned technology?
About our Expert