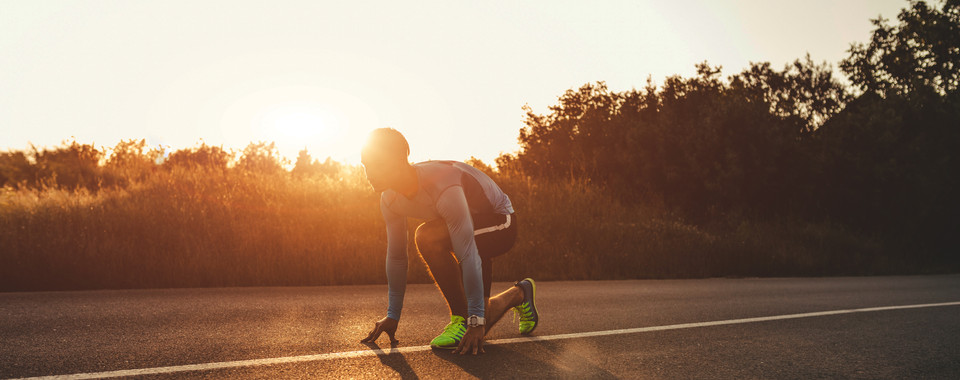
Jun 5, 2025 // Lill Haase
Demand Planning in Vehicle Logistics – Set the Pace
Bring structure to your yards and workshops. Forecast better. Act faster. Stay in control. Discover how INFORM enables smarter vehicle logistics.
Nov 22, 2016 Luisa Walendy
ShareCan you imagine a vessel that has a hull big enough to simultaneously host all 8 round-of-sixteen matches of the all European Football Championship Series? This vessel, the MV Parsifal, is 870 feet long and nearly 177 feet high, and can transport about 6,000 cars. Currently sailing around Western Europe, the world´s largest car carrier makes stops at some of the biggest vehicle terminals, one being Zeebrugge, Belgium. Last year, nearly 2.5 million cars were shipped through the Port of Zeebrugge.
With multiple vessels calling on the vehicle terminals at Zeebrugge at one time, finding dock space isn’t the only logistical challenge that vehicle terminal operators face. With time as a critical factor, yard operators must orchestrate all movements across the terminal including the unloading, parking, and loading efforts. To boost efficiency and throughput, yard operators should follow these five tips:
To find the optimal parking space for each car, it is important to consider not only where you have space on the yard, but take into consideration what the next steps are for that individual vehicle. Will the vehicle undergo modification? Is the vehicle damaged? What is the next mode of transportation? These questions must be considered to optimize parking and keep costly kilometers off the odometer.
If the vehicle does need to be modified before shipment, modifications and maintenance dates must be integrated into the parking planning. The assembly deadlines are prioritized in consideration of the current logistics and inventory situation. By doing so, personnel and material resources can also be efficiently planned.
Once ready for outbound transit, the aim is to reach maximal capacity on the different transportation means such as train or vessel. This can be accomplished through intelligent vehicle grouping as well as load planning to ensure each load leaving through the gates is maximized, which in turn increases throughput.
As a vehicle yard operator or employee you will likely have already recognized that the space on the yard and the management of vehicle movements are no any longer manageable manually or in excel sheets. The processes are too complex and the customers´ requirements too high. Each delay brings with it unnecessary increased costs. To plan the supply chain on the yard efficiently, the cars´ position and status must always be readily available and transparent. Using visualization, it is possible to not only increase overall yard transparency but also track individual VINs through their life cycle on the vehicle yard. The transparency of each car and process is the basis for optimal planning and controlling processes.
The planning on a vehicle yard has to be dynamic and flexible. All too often, unpredictable events happen which cannot be accounted for by a static plan. For example, if workers in the modification center call in sick or a parts shipment is delayed, it is imperative to be able to quickly react to these changes to reshuffle the work to be completed and mitigate potential bottlenecks and delays. Real time planning gives vehicle yard operators the flexibility that they need to react to the dynamic work environment.
As these unpredictable events mostly result from the up- and downstream processes in the vehicle´s supply chain, it helps to take all processes into account. By utilizing tools that strategically design the logistical network and can centrally manage the entire vehicle distribution life cycle, yard operators can help to ensure smooth processes within the yard as well as meet customer demand and delivery commitments. Central process automation and optimization is also possible by compiling the data of all these logistics processes in one system.
The first three tips underline the fact that planning vehicle yard processes is complex and not manageable by one or more human beings. Intelligent yard management can manage yards and link different functions as well as optimize the processes in order to reduce costs and boost efficiency. The solutions control the ongoing processes on the yard and reschedule automatically in real-time. Further, they plan the processes of the following days.
In addition, an intelligent system can generate key performance indicators to monitor the yard´s performance, the reporting and the billing of the yard services. The whole data exchange with OEMs, suppliers and other partners can be performed by one data interface.
Quality and punctuality are important factors on a vehicle yard to satisfy the customer´s needs. In contrast to other logistics, the processes are highly unique due to the damage handling and hold management. A car is often a “work in progress” as it receives its accessories and full customization close to the customer´s location. With the processes as well as the physical yards becoming increasingly complex, software is key to optimize logistics by considering many parameters on the yard, connecting to up- and downstream logistics processes and offering real-time transparency.
About our Expert